Summary:...
Automation has revolutionized various industries, streamlining processes, increasing efficiency, and reducing human error. At the core of many automated systems lies the planetary gear motor, a vital component that converts electrical energy into mechanical power. When it comes to selecting the right planetary gear motor for your automation needs, several factors must be considered. In this article, we will explore key considerations to ensure you make an informed decision.
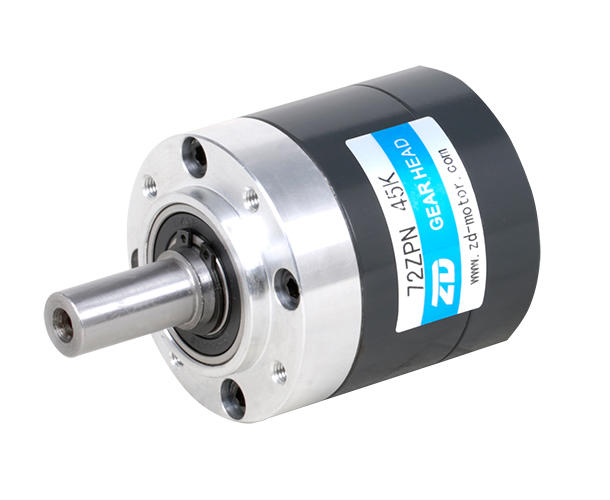
1. Torque Requirement:
The torque requirement of your application is a critical factor in selecting a
planetary gear motor. Consider the load that the motor needs to drive and calculate the required torque. Ensure that the selected motor provides sufficient torque to handle the load without compromising performance.
2. Speed Range:
Different automation applications have varying speed requirements. Determine the speed range needed for your system and choose a planetary gear motor that can operate within that range. Consider both the maximum and minimum speeds required to ensure optimal performance.
3. Size and Compactness:
Space constraints are common in automation systems, especially those involving robotics and machinery. Planetary gear motors are known for their compactness and high power density, making them suitable for tight spaces. Consider the physical dimensions of the motor and choose a compact design that fits within your application's limitations.
4. Efficiency:
Efficiency plays a crucial role in automation systems, as it directly affects energy consumption and overall system performance. Look for planetary gear motors with high efficiency ratings to minimize energy losses and maximize the effectiveness of your automated processes.
5. Gear Ratio:
The gear ratio determines the relationship between the motor's input speed and the output speed. It plays a significant role in achieving the desired torque and speed requirements. Evaluate the gear ratio options available for a planetary gear motor and select one that aligns with your application's demands.
6. Durability and Reliability:
Automation systems often run continuously or for extended periods. Therefore, the durability and reliability of the planetary gear motor are essential considerations. Look for motors built with high-quality materials and designed for long-lasting performance. Consider factors such as bearing type, sealing mechanisms, and overall construction to ensure a reliable and robust motor.
7. Precision and Control:
Certain automation applications require precise control over speed, position, and torque. If your application demands high precision, choose a planetary gear motor with features like backlash reduction, low hysteresis, and smooth operation. Such motors enable precise control, contributing to the accuracy of your automated processes.
8. Environmental Considerations:
Consider the environmental conditions in which the planetary gear motor will operate. Factors such as temperature, humidity, and exposure to dust or chemicals can impact motor performance and longevity. Ensure that the motor you choose is suitable for the environmental conditions it will encounter.
9. Noise and Vibration:
Excessive noise and vibration can affect the overall efficiency and performance of an automation system. Look for planetary gear motors designed with noise and vibration reduction features, such as precision gearing, advanced lubrication systems, and damping mechanisms. These features contribute to a quieter and smoother operation.
10. Cost Considerations:
Finally, consider the cost of the planetary gear motor and its overall value for your automation needs. While it's essential to stay within budget, prioritize the motor's performance, reliability, and long-term cost-effectiveness over upfront costs. A high-quality motor may have a higher initial investment but can save costs in maintenance, downtime, and energy consumption in the long run.
In conclusion, choosing the right planetary gear motor for your automation needs requires careful consideration of torque requirements, speed range, compactness, efficiency, gear ratio, durability, precision, environmental factors, noise and vibration, and cost. By evaluating these factors, you can make an informed decision that ensures optimal performance, longevity, and efficiency in your automation system.