Summary:...
1. The motor is only part of the efficiency equation
First of all, before purchasing a motor, it must be clear that the motor can only reach one-sixth of the total energy loss potential of the electromechanical drive system. And, more importantly, it is usually not even the least efficient part. Mechanical equipment, such as external transmission components, is much less efficient than electrical equipment. So, first look there to find your biggest energy savings.
2. By transforming the entire transmission system, you can use a smaller motor and save more
Now, you may be using a motor with a specific power rating to produce a specific output from the drivetrain. You may be pleasantly surprised to find that sufficient efficiency is obtained through gearboxes, drives and external transmission components. Therefore, you can save additional costs by purchasing a low-horsepower motor. E.g:
Before: 45kW load ÷ 53.5% efficiency = 84.1kW (using 90kW motor)
After: 45kW load ÷ 72.5% efficiency = 62.1kW (using 75kW motor)
3. The fit of motor and equipment application
Even if all other components are as efficient as possible, just placing a high-efficiency motor on the production line may not automatically solve all your energy problems. In this case, a high-efficiency motor designed for this type of application is used, and an integrated brake of the appropriate size is used. In addition, where possible, use the smallest motor for the application, with a load close to 80% and running as close to the nameplate efficiency as possible.
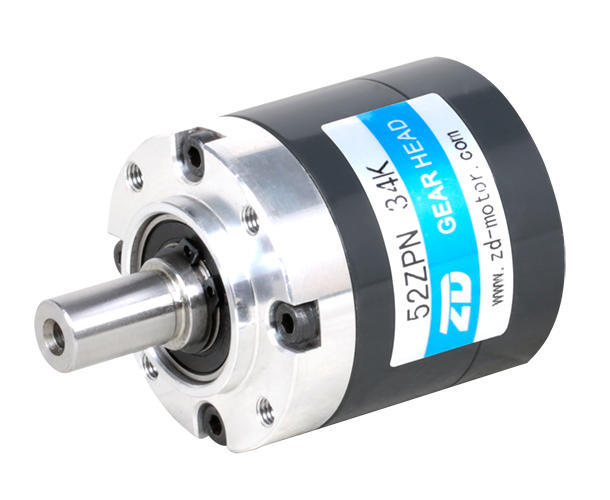
4. Mechanical efficiency is also important
Worm gear reducers are common in the industry, and their efficiency ranges from 50% to 88%, depending on the number of teeth or gear ratio of the worm gear. Their inefficiency is due to the sliding gear contact friction, which causes most of the energy to be wasted through heat. On the contrary, the hardened bevel gear motor device uses rolling friction, so each stage only loses 1.5% efficiency, which is 95.5% efficiency.
Although the initial cost of hardened bevel gear motors is higher, they will save energy throughout the life of the system. If you are an end user, please consider specifying a helical-bevel gear reducer the next time you purchase equipment for your factory.
5. The
planetary gear motor eliminates more efficiency losses.
Compared with general flexible transmission systems, gear motors essentially improve efficiency. Since the geared motor contains a motor that is precisely aligned with the reducer, the connection efficiency is close to 100%.