Summary:...
Servo and stepper motors have the same structure and use the same operating principle. Both motors include a permanent magnet rotor and a stator with wound windings. Both are operated by electricity or applying DC voltage to the stator windings, which means that the rotor moves. However, this is the only similarity between servo and stepper motor.
Stepping motor drive method
Stepper motors have 50 to 100 poles and are two-phase devices. In contrast, servo motors have 4 to 12 poles and are three-phase devices.
The stepper motor driver generates a sine wave with frequency that changes with the speed, but the magnitude is constant.
Servo drives, on the other hand, generate sine waves with frequency conversion and magnitude, which allows them to control speed and torque.
Stepping motor control method
The traditional stepping motor advances to a certain number of pulses to move after receiving an instruction, which is related to distance. Stepper motors are considered open loop systems because they lack a feedback mechanism to confirm that the target position has been reached. The servo motor will also move after receiving the command from the controller. Contrary to the operation of an open-loop stepper motor system, the servo motor is a closed-loop system with a built-in encoder that constantly contacts the controller, which makes any adjustments needed to ensure that the target position is reached.
In a stepping motor system, if the available motor torque is not enough to overcome the load, the motor will stop or skip one or more pulses, creating a difference between the ideal position and the actual position reached. To avoid this problem, stepper motors are usually large in size to ensure that there is a surplus between the worst load torque and the motor's available torque. In addition to increasing the size of the motor, there is another option. By adding an encoder and running in a servo mode, the stepper motor system can obtain position monitoring and control, just like a servo motor.
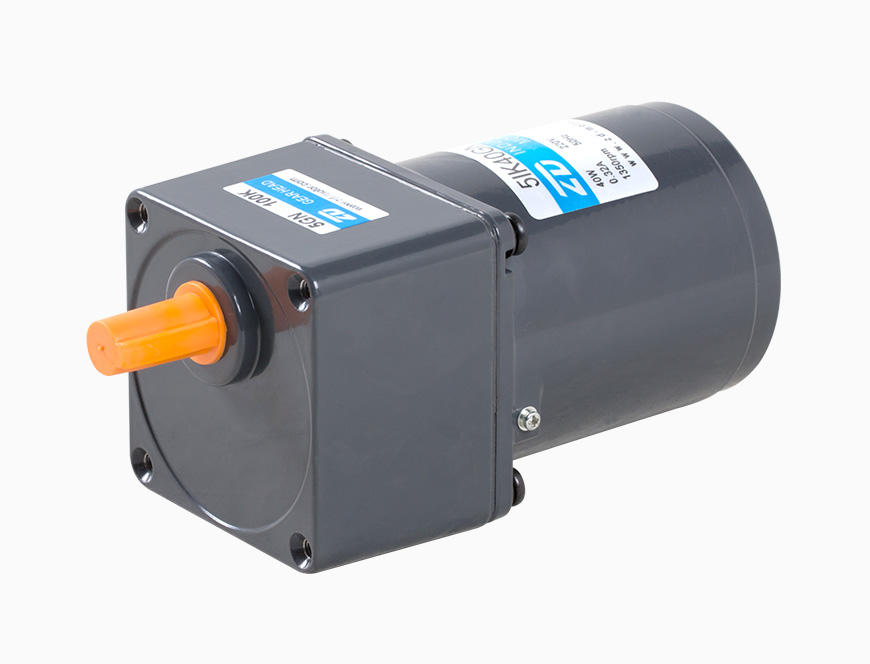
The most straightforward way to run a stepper motor in closed-loop mode is to compare the theoretical position that has been obtained based on the number of steps, and the actual position based on the encoder feedback. If there is a difference between the target and actual position, the controller will initiate a corrective action.
Although the above method is reactive, after the movement is completed, the position of the motor is modified. A closed-loop stepper motor can continuously monitor the difference between the number of position steps and the encoder feedback (this is typically embedded in the load) . With continuous feedback, compensation can be completed in real time, by increasing the pulse frequency, temporarily increasing the current, or adjusting the step angle.
In closed loop mode, the third way to run a stepper motor is to use sinusoidal commutation. If the stator and rotor magnetic fields are not properly aligned, the encoder adjusts the motor current to accurately match the required torque to move or control the load. Because feedback is used to control torque, by monitoring motor current, this mode is sometimes called servo control. In the servo control mode, the stepper motor actually behaves like a high-pole servo motor. However, there is no noise and resonance like traditional stepper motors, which provides smoother movement and more precise control. Because the current is dynamic instead of a constant value like the traditional stepper motor, the problem of motor heating is greatly avoided.
Closed-loop stepper motors eliminate many defects of traditional open-loop systems, making them similar in performance to servo motors. In applications requiring high speed, high speed and high torque, and the ability to handle changing loads, the performance of the servo motor is due to the closed-loop stepper motor.