Summary:...
As a vulnerable part, the life of the motor (especially the brush motor) component is relatively short for the entire motion system. Therefore, it is very necessary to understand some precautions when using the motor.
1. Machining of motor (gearbox) shaft: According to different loads, customers often need to process the output shaft, such as: punching, milling, keyway, etc. The safest method is to fix the load on the shaft through the top wire. For further tightening, two top wires with an angle of 90° can be used for fixing. If the output shaft must be processed, it must be ensured that the axial and radial forces on the output shaft do not exceed the indicators given in the parameter table during the machining process, otherwise the bearing of the output shaft will easily be damaged. In the worst case, the shaft vibration increases, in the worst case, the motor and gear box are completely unusable, and the most serious may even damage the encoder at the back of the motor and cause the complete set of products to be scrapped.
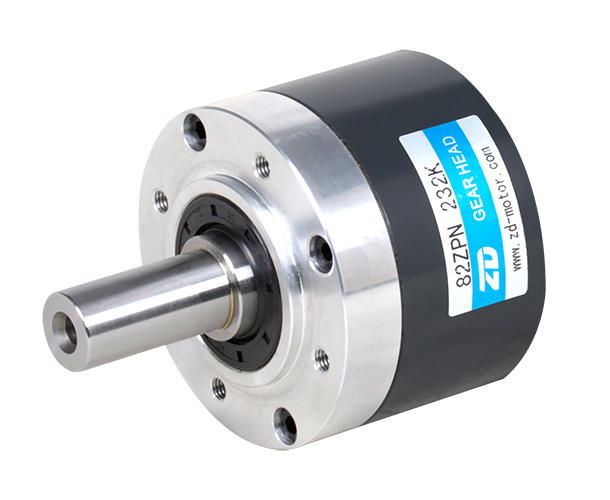
2. Motor locked-rotor: After the motor is locked, the consumed current reaches the maximum value and all the electrical energy is converted into heat. This may cause the motor temperature to rise sharply in a short period of time. There will be serious consequences such as magnet demagnetization and coil short circuit. Motor locked-rotor current = voltage applied to the motor/motor terminal resistance
3. Soldering lugs at the end of the motor: For a brushed motor, there are two metal lugs at the end to connect to the power supply. The solder tabs have a certain degree of flexibility, but they cannot be bent repeatedly. More than three times may break